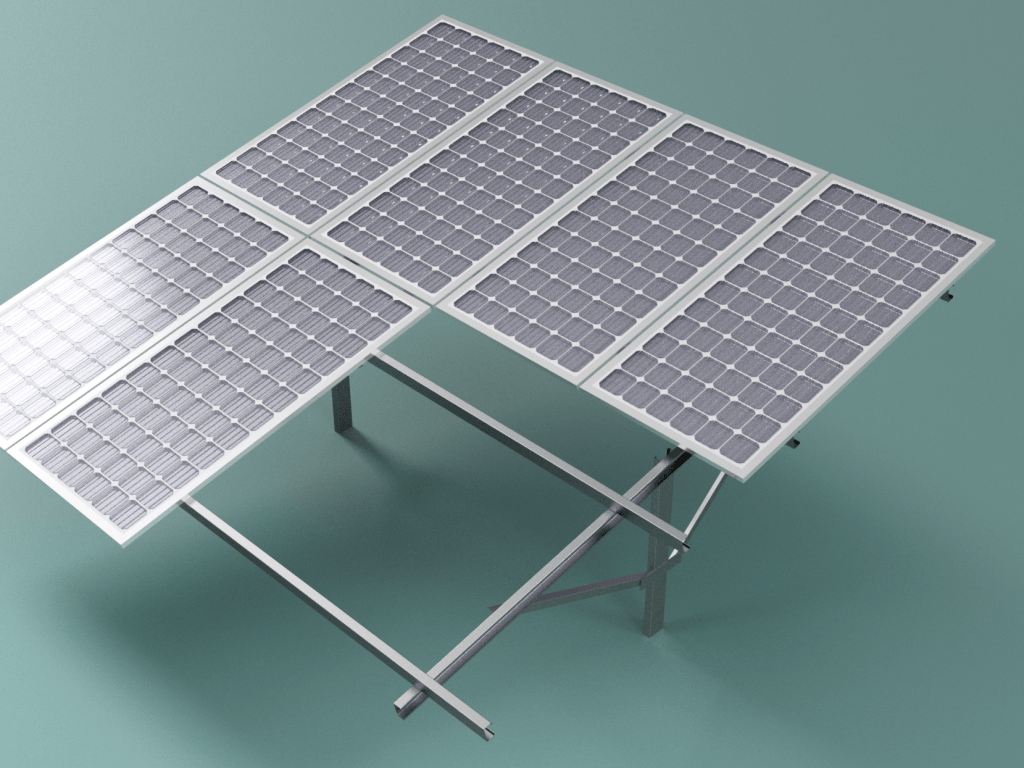
I. Select the Right Land
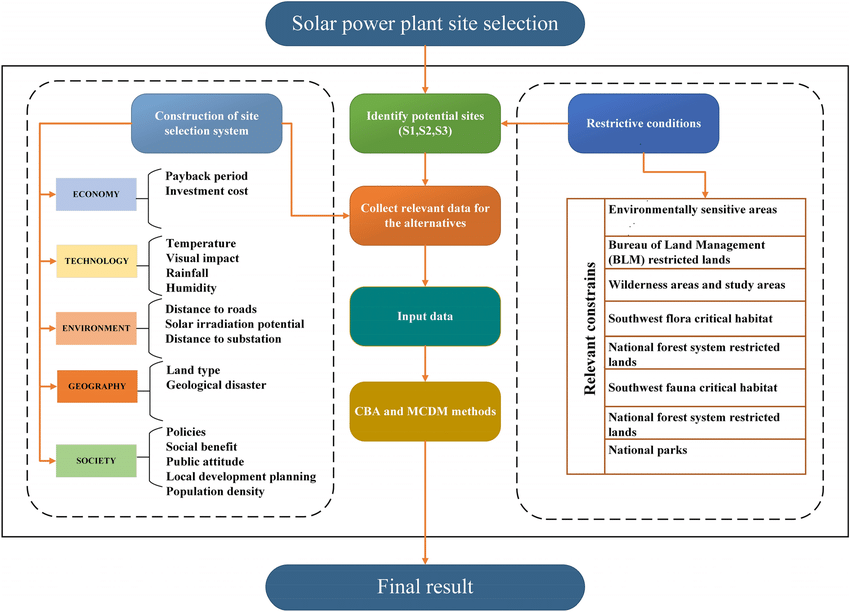
Choosing the right piece of land is a critical first step to lower solar construction costs. The land has certain requirements and criteria that must be met before building a solar project on it, covering factors like:
- Topography and terrain
- Electrical infrastructure access
- Wildlife impact
The land should ideally be:
- Reasonably cleared and level
- Within 1-3 miles of a substation
- Within 1 mile of a three-phase power line
It’s important not to rush into leasing land only based on an attractive price. Being selective about your future solar site may cost more upfront and involve competition with other solar developers, but the wrong land could raise financial implications later on.
For example:
- Contaminated lands bring liability and regulatory issues
- Prolonged construction time and higher costs
Conducting site evaluations with a geotechnical investigation plan helps mitigate risk:
Site Condition Evaluations | Importance |
Slope stability analysis | Ensures proper foundation design |
Sediment control testing | Informs storm water management system |
Subgrade examinations | Verifies adequate ground bearing pressure |
Being selective about your solar land site may cost more upfront, but saves money in the long run by preventing avoidable construction issues. Analyse the size, shape, and terrain to determine if the land meets critical criteria. Don’t rush into a land lease solely based on an attractive price.
II. Let the Land Inform Design
Once you have secured the right land, conduct thorough site evaluations to inform the solar project design. This helps reduce unexpected issues arising during construction that add costs. Key steps include:
Geotechnical Investigations
Perform detailed geotechnical studies of the site including:
- Slope stability analysis
- Soil corrosivity measurements
- Identifying soil bearing pressure and capacities
This data helps determine:
- Proper foundation dimensions
- Appropriate ground preparation
- Necessary sediment erosion controls
Having accurate geotechnical inputs prevents under-engineering foundations that fail or over-building that wastes money.
Racking and Mounting Design
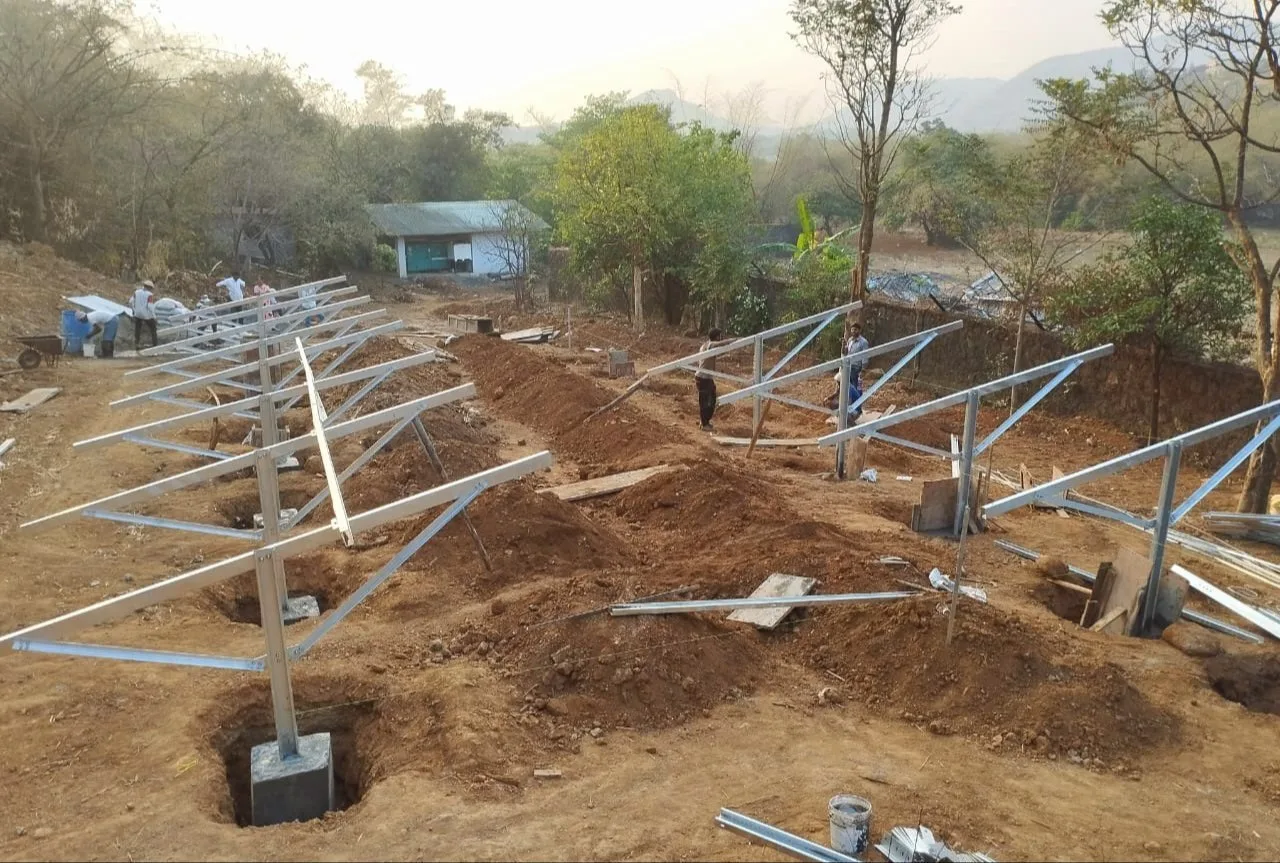
The site’s soil and terrain conditions should also guide designing the solar racking system:
- Account for slope, load capacities and wind shear
- Ensure proper anchor sizing and embedment depths
Carefully matched racking avoids unnecessary costs from:
- Insufficiently anchored structures failing in high loads
- Oversized racking increasing materials, construction and land use
Storm Water Management Evaluation
- Assess site topography and hydrology
- Model potential erosion volumes
- Design effective grading and sediment control measures
Preventing runoff and erosion problems during construction protects water quality and avoids costly mitigation.
In sum, informed solar design optimized for the site’s unique properties saves money during builds and over asset life cycles.
III. Choose Reliable Equipment
Selecting durable, high-performing equipment suited for the solar project can help efficiently meet construction targets and budgets. Best practices include:
Vendor Evaluation
Thoroughly assess potential vendors and suppliers on:
- Product quality and durability
- Warranties and maintenance terms
- Past performance meeting specifications
This reduces unexpected costs from fixes or change orders.
Specification Setting
Clearly define project performance requirements and operating conditions including:
- Weather resilience testing (wind, humidity, temperatures)
- Critical load capacities and safety factors
- Compliance with all applicable standards
Equipment unable to meet specifications can slow progress or require replacements.
Testing and Inspection
Validate equipment condition and capabilities through:
- Performance verification testing
- Quality control inspections at factories and upon delivery
- Operational trial runs before full deployment
This prevents integrating defective components into builds.
Preventative Maintenance
Follow all manufacturer recommended upkeep like:
- Component lubrication and cleaning
- Tightening loose connections
- Tuning and calibration
Proactively caring for equipment prevents breakdowns or failures that are more disruptive to fix during active construction.
Choosing robust, durable equipment tailored to the project’s specific demands increases construction efficiency and asset longevity while lowering lifetime equipment costs.
IV. Simplify Racking Installation
Streamlining the solar racking installation process through thoughtful design and planning cuts costs by maximizing efficiency. Useful techniques include:
Adjustable Components
Specify racking with some flexibility to accommodate variability in site conditions like:
- Slope grade changes
- Subtle foundation shifts
- Minor anchor position adjustments
This avoids expensive time delays from disassembly or holes requiring re-drilling.
Installation Work Plans
Create detailed work plans mapping the sequential process including:
- Equipment and tool requirements
- Labour needs and assignments
- Anticipated production rates
Thorough plans allow coordinating teams and deliveries for smooth flows, preventing downtime from missing items.
Streamlined Hardware
Prioritize racking using simplified components like:
- Universal clamps fitting multiple module types
- Single bolt designs
- Integrated ground bonds
Simpler assemblies with fewer unique parts quicken overall mounting.
Specialized Equipment
Leverage purpose-built tools for efficiency gains on repetitive tasks like:
- Auto-dispensing auger rigs for drilling pile foundations
- Custom jigs ensuring consistent positioning
- Lifting aids for positioning sections
The right equipment prevents injury and enhances productivity.
Careful coordination, adjustable parts allowing adaption, and streamlined installations prevent complications that sap field productivity – saving costs with efficient solar racking assembly.
V. Control Construction Budget
Carefully managing the construction budget helps avoid cost overruns that erode project returns. Best practices include:
Early Cost Estimation
Develop initial budgets during early planning using expected:
- Equipment, material, and labour expenses
- Permitting, grid connection, and inspection fees
- Site preparation and installation costs
- Lease payments
Regularly update these projections with real quotes as specifics firm up.
Risk Assessment
Proactively evaluate uncertainties that may impact costs like:
- Inclement weather delays
- Potential supply chain disruptions
- Changes in material pricing
- Community complaints
Identify mitigations to contain budgets despite issues.
Contingency Funds
Incorporate 5-10% contingencies within budget estimates for the inevitable unplanned events on large builds. This prevents scrambling to fund surprises.
Value Engineering
Continuously identity ways to trim costs like:
- Sourcing substitute materials
- Simplifying designs
- Using more efficient construction techniques
Savings from value engineering provide additional buffers.
Change Control
Carefully evaluate any project changes for cost/benefit before approval to prevent scope creep.
Ongoing cost oversight, planning for uncertainties, and continuous optimization prevents overspending, keeping solar projects economically viable.
VI. Account for Soft Costs
“Soft costs” like permitting, financing, and labour add up. Strategies to control these expenses include:
Streamlined Permitting
- Research local solar ordinances in detail
- Prepare thorough permit packages
- Use expediters to ease process
Understanding requirements and properly completed submissions prevent delays from application issues.
Efficient Procurement
- Comparison shop equipment and materials
- Leverage online supply marketplaces
- Optimize logistics like shipping modes
Casting a wide net surfaces best pricing and responsiveness.
Labour Optimization
- Cross-train workers on multiple tasks
- Use crews balancing experience levels
- Incentivize on-time delivery
Flexible, motivated crews prevent downtime and inefficiencies.
Strategic Sourcing
- Buy cables, connectors in bulk
- Seek winter off-season discounts
- Favour modular components
Order consolidation and tactical timing reduce supply chain expenses.
While some soft costs are fixed, focus on streamlining variable expenses.
Cost Containment Strategies
Area | Savings Approach |
Permitting | Submit complete packages |
Procurement | Leverage marketplaces |
Labour | Reward on-time work |
Sourcing | Buy at scale in off-seasons |
Get ahead of soft costs early in planning to protect project profitability.
VII. Assemble Experienced Team
The right solar project team is crucial for on-time, on-budget delivery. Best practices for assembly include:
Diverse Expertise
Staff key roles with experts in areas like:
- Solar design engineering
- Procurement and supply chain
- Project planning and controls
- Grid integration and commissioning
This breadth covers the multifaceted competencies vital for success.
Proven Track Records
Validate capabilities by examining:
- Years in industry
- Projects successfully delivered
- Client references
- Safety and performance metrics
This reduces risk of underperforming personnel sinking progress.
Aligned Incentives
Structure contracts promoting shared project success through:
- Bonuses for schedule and budget achievement
- Penalties for missteps
- Profit sharing
Incentive alignment prevents finger pointing during crunch times.
Scalable Resourcing
Ensure capacity to flex expert personnel levels up and down as activity fluctuates during project phases. This cost-effectively right-sizes labour.
Responsiveness Training
Conduct emergency response simulations preparing crews to smoothly handle incidents like storms or injuries if they arise with minimal safety and cost impacts.
Investing in the right expertise, experience, motivation and responsiveness in a solar build team pays dividends through maximized efficiency and risk reduction over the project lifecycle.
VIII. Prepare Contingency Funds
Despite best-laid plans, unexpected events during solar construction add costs. Maintaining contingency funds mitigates overruns threatening project viability. Best practices include:
Historical Spending Analysis
Examine past projects to estimate emergency cost frequencies in areas like:
- Permitting delays
- Weather downtime
- Equipment failures
- Materials pricing changes
These insights quantify contingency targets.
Probability Impact Matrices
Map identified risk events by likelihood and potential cost severity to prioritize responses and gauge required reserves.
Risk | High Likelihood | Low Likelihood |
High Cost | Permit denials | Foundation redesigns |
Low Cost | Inspections | Minor repairs |
Ongoing Reassessment
Re-evaluate required contingency amounts and probability estimates at major milestones as uncertainties resolve over the project timeline.
Contingency Tracking
Implement formal change control processes ensuring contingency funds only applied to eligible unforeseen costs rather than scope expansions.
Proactively earmarking reserves for the inevitable unknowns, continually refining estimates, and tightly controlling drawdowns ensures access to emergency funding without tapping capital required for planned activities. Sized correctly, contingencies become insurance policies enabling construction progress despite surprises.