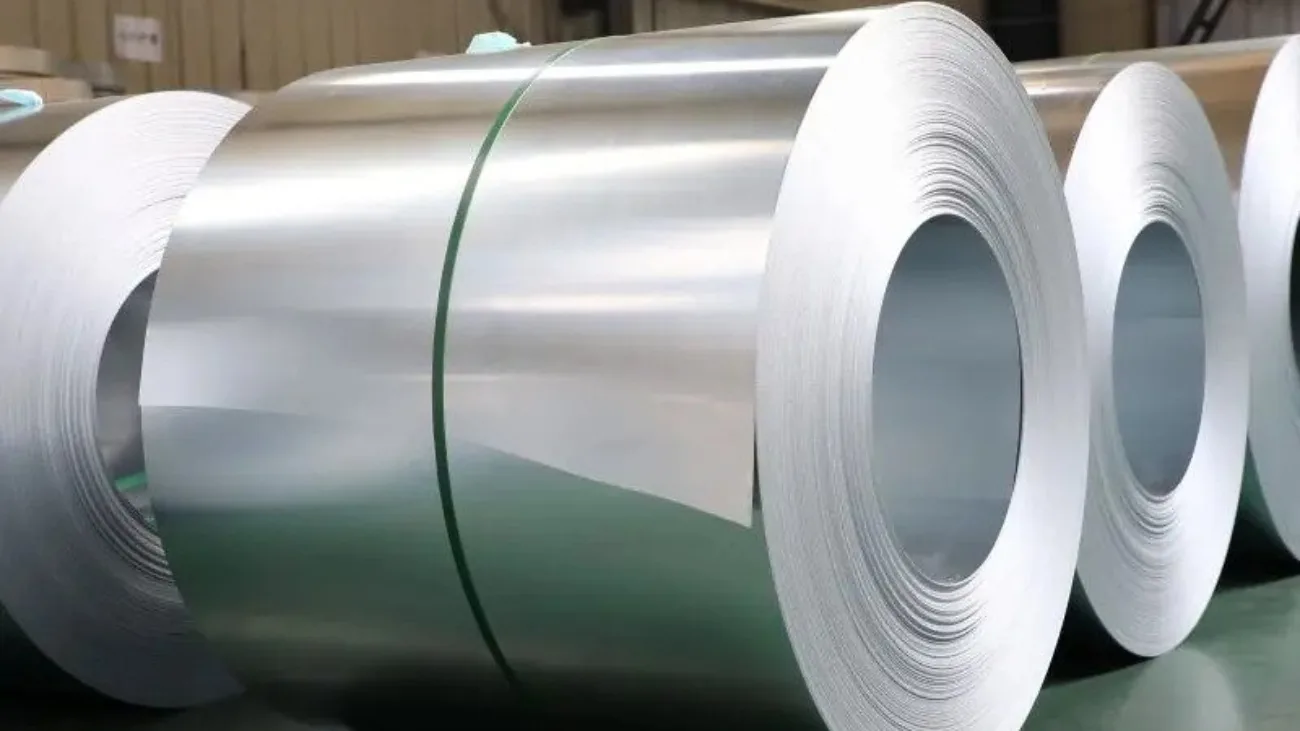
I. Introduction
Galvanized and hot dip galvanized coatings are commonly used for corrosion protection of solar mounting structures. The choice between galvanized solar mounting frames and hot dip galvanized solar rails depends on factors like cost, longevity, and ease of application.
The key differences between galvanized and hot dip galvanized coatings for solar mounting structures:
- Type of zinc coating
- Surface preparation requirements
- Resulting surface texture and finish
- Corrosion resistance performance
A summary of the differences is provided in the table below:
Criteria | Galvanized Coating | Hot Dip Galvanized Coating |
Process | Electroplating, thermal spray | Hot dip immersion in molten zinc bath |
Surface preparation | Degreasing, pickling | Degreasing, pickling, fluxing |
Coating texture | Smooth, sharp finish | Rough finish |
Corrosion protection | Moderate | Excellent |
Galvanized coatings are applied by methods like:
- Electroplating
- Thermal spray of molten zinc
- Mechanical plating
These provide a smooth, uniform finish on solar mounting components like frames, brackets, and fasteners.
Structura will provide a Hot dip galvanizing involves dipping prepared steel components in a bath of molten zinc to form zinc-iron alloy layers. This provides excellent corrosion resistance but results in a rough texture.
By understanding the key differences, solar project developers can select the optimal corrosion protection method for their specific solar mounting requirements.
II. Galvanized Coatings for Solar Mounting Structures
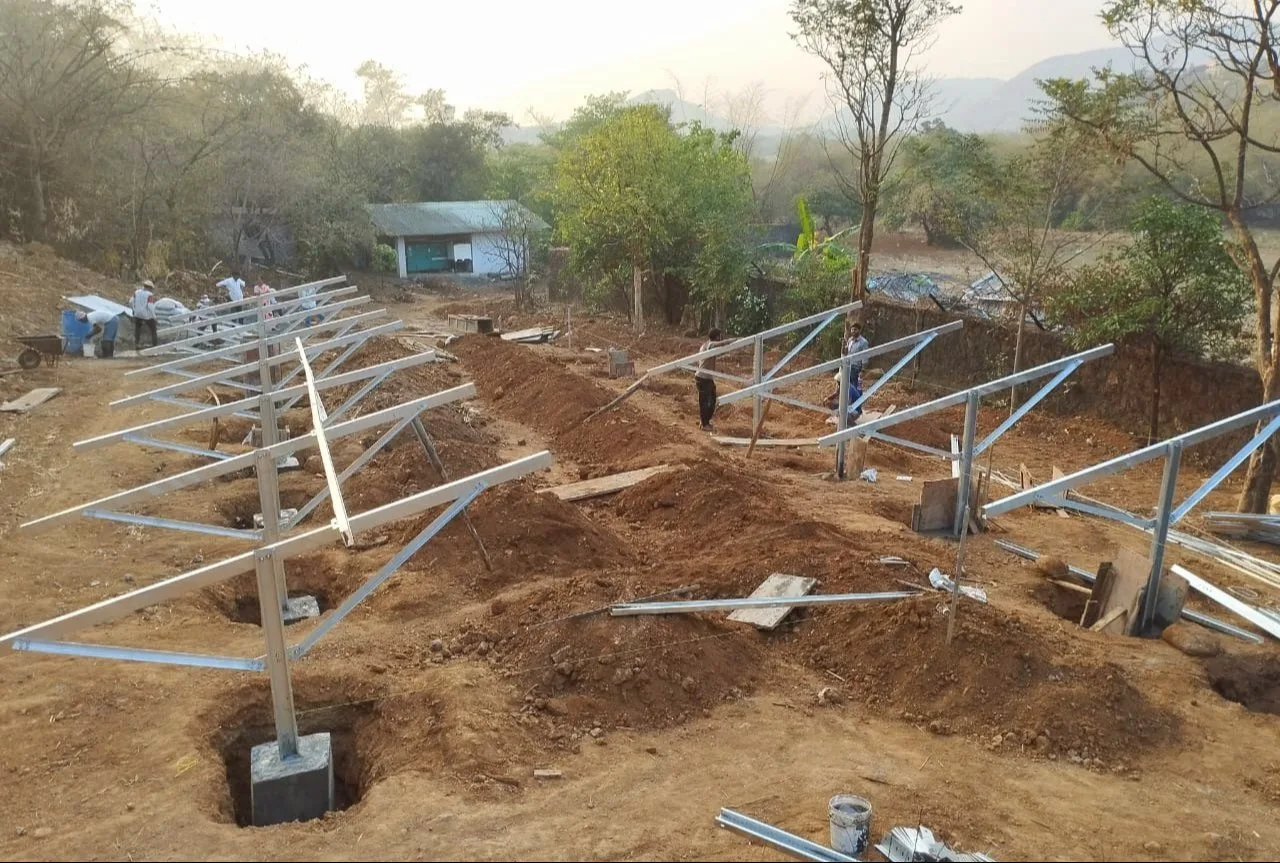
Galvanized coatings are commonly applied to solar mounting components like:
- Solar module frames
- Solar array brackets
- Solar structure bolts
Galvanized coatings provide moderate corrosion protection with a smooth finish.
The main galvanizing processes are:
- Electroplating – Uses electric current to deposit zinc onto solar components
- Thermal spray – Sprays molten zinc onto solar panel parts
- Mechanical plating – Deposits zinc through mechanical energy
Benefits:
- Lower cost
- Uniform smooth finish
- Good for steel solar anchors and mounting posts
Limitations:
- Less corrosion protection than hot dip galvanizing
- Not suitable for high corrosion environments
Overall, galvanized coatings are cost-effective for solar structures not exposed to extreme weather conditions. The smooth finish also allows efficient installation of solar modules.
III. Hot Dip Galvanized Coatings for Solar Arrays
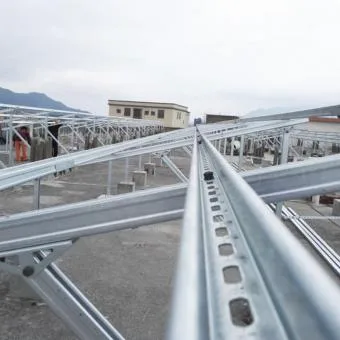
Hot dip galvanizing is commonly used to protect large solar array structures and components like:
- Solar array rails
- Solar panel clamps
- Solar tracking braces
The hot dip galvanizing process involves:
- Surface preparation – Degreasing, pickling, and fluxing
- Dipping in molten zinc bath to form zinc-iron alloy layer
- Inspection of coating quality
Benefits:
- Excellent corrosion resistance
- Withstands extreme weather environments
- Long service life for solar mounting hardware
Limitations:
- Rough surface finish
- Higher cost than galvanizing
Hot dip galvanized coatings provide maximum corrosion protection for large solar arrays and mounts installed in coastal, industrial, and severe climate environments. The service life can exceed 25 years.
IV. Surface Preparation of Solar Mounting Components
Proper surface preparation is essential prior to applying galvanized or hot dip galvanized coatings on solar mounting hardware. The main preparation steps include:
- Degreasing – Removes oil, grease and dirt from surfaces like:
- Solar module frames
- Solar tracking drive arms
- Solar clamp bolts
- Pickling – Uses acid solution to remove iron oxide and mill scale from:
- Solar structure I-beams
- Solar foundation anchor bolts
- Fluxing (for hot dip galvanizing) – Applies protective flux coating to prevent oxidation of steels like:
- Solar torque tube shafts
- Solar array roller pins
Effective surface preparation allows maximum adhesion and corrosion protection from the galvanized or hot dip galvanized coatings.
It is crucial to remove all traces of oil, grease, rust, scale and other contaminants from the steel surface through thorough cleaning, pickling, and fluxing steps.
This ensures optimal zinc coverage and corrosion resistance for the solar mounting hardware over decades of service.
V. Corrosion Protection with Zinc Layers
The key purpose of galvanized and hot dip galvanized coatings is to provide corrosion protection for steel solar mounting components.
The zinc coating protects the underlying steel in two ways:
- Barrier protection – The zinc coating forms a physical barrier preventing corrosion agents like oxygen, moisture and chloride ions from reaching the steel.
- Cathodic protection – If the zinc coating gets scratched, the zinc sacrifices itself and corrodes first instead of the underlying steel. This is due to the electrochemical properties of zinc.
During hot dip galvanizing, iron on the steel surface reacts with the molten zinc bath to form protective zinc-iron alloy layers.
Prior pickling to remove iron oxide and mill scale allows better contact between the steel and molten zinc to form uniform alloy layers.
The resulting zinc coating provides excellent corrosion resistance for steel solar mounting hardware, even in harsh outdoor environments with high humidity, salt spray or industrial pollutants.
Proper surface preparation and quality hot dip galvanizing processes optimize the protective zinc layer thickness and life span.
VI. Finishing and Inspection of Solar Mounts
The final steps for galvanized and hot dip galvanized solar mounting components involve:
- Finishing to achieve the desired surface texture
- Inspection to ensure coating quality
- Galvanized coatings have a smooth, sharp finish suitable for:
- Solar array frames
- Solar tracker gears
- Solar PV module clamps
The smooth finish allows easy cleaning and maintenance.
Hot dip galvanizing produces a rough surface finish. The zinc-iron alloy layers form crystals that grow outward as spiky dendrites.
This rough texture provides optimal adhesion for paints and sealants when applied on:
- Solar torque tubes
- Solar support strut channels
- Solar tracker rails
Thorough inspection verifies coating thickness, integrity and uniformity.
The visual contrast between galvanized and hot dip galvanized finishes provides a quick way to identify the corrosion protection method used on solar mounting components.
Proper finishing and inspection ensures long-lasting weather resistance and durability.
VII. Conclusion
Both galvanized and hot dip galvanized coatings offer effective corrosion protection for steel solar mounting structures.
Galvanized coatings provide good weather resistance at lower cost for solar components like:
- Frames
- Brackets
- Fasteners
Hot dip galvanizing is the optimal choice for heavily loaded structural solar mounts and arrays in harsh environments, including:
- Coastal areas
- Industrial zones
- Deserts
Proper surface preparation, zinc coating method, quality control and finish are crucial to achieve the desired longevity and return on investment.
By selecting the appropriate galvanizing method for the solar application and environment, developers can minimize maintenance costs while maximizing power output over decades.
Regular inspection of zinc coatings enables proactive maintenance to avoid any coating damage or corrosion issues.
Overall, both galvanized and hot dip galvanized treatments provide reliable, low-maintenance corrosion protection for a wide range of solar power projects.