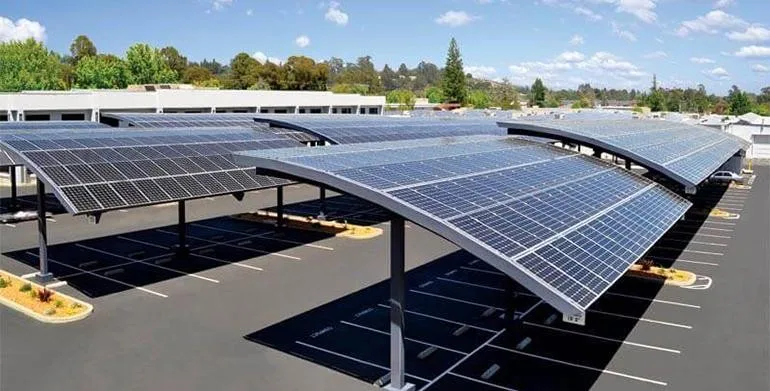
I. Solar Carport Efficiently Use Space
Our solar carports system are an innovative solution that utilizes existing spaces efficiently to generate clean energy. By installing solar panel canopy structures over parking lots and other areas that are already being used, solar carports are able to produce renewable power without taking up additional land.
Some key ways that solar carports leverage space efficiently include:
- Using unused real estate: Solar carports are mounted over spaces that are often underutilized.
- Parking lots
- Driveways
- Patios
- Sidewalks
- Maximizing horizontal spaces: The wide, flat canopy structures of solar carports are perfect for covering spaces used for parking and storage.
- Making double use of necessary structures: Solar carports shelter vehicles, equipment, and people from the elements while also collecting energy from the sun.
Benefits | Details |
No lost land usage | Solar carports added over existing infrastructure don’t require using up green spaces or acquiring additional land |
Increased productivity | The shaded spaces under solar carports allow assets like vehicles to operate more efficiently |
Dual-use infrastructure | Solar carports do “double duty” by generating renewable power in spaces that serve other primary purposes like parking |
The next time you walk through a parking garage or outdoor lot, consider the potential to install solar canopies or carports. By embracing the available but overlooked real estate, businesses and towns can generate clean energy efficiently through solar technology that maximizes existing space usage.
II. Solar Carports Reduce Costs
Our installing process of solar carports delivers major cost savings in two key areas:
Energy Expenses
- Solar panels generate clean electricity, offsetting power that would otherwise need to be purchased from the grid
- Businesses can save thousands per year on electricity bills with an appropriately-sized solar carport system
- Solar carports can power adjacent buildings, electric vehicle charging stations, outdoor lighting, and other facilities
Infrastructure Costs
- Solar carports serve dual purposes, eliminating the need for separate structure investments just for power generation
- Building a solar carport over an existing parking lot costs less than adding a rooftop solar array
- Multi-capability design reduces need for other weather/UV protection measures
Additional financial benefits stem from:
- Lower maintenance needs than ground mount solar or traditional rooftop systems
- Increased productivity from shaded working/storage areas protected from elements
- Enhanced property value from improved generating capacity and modernized facilities
Cost Savings Area | Solar Carport Advantage |
Energy expenses | Clean solar energy offsets grid purchases |
Infrastructure costs | Dual-use structures reduce additional builds |
Maintenance | Easy ground-level access minimizes upkeep |
Productivity | Weather protection increases asset efficiency |
Property value | Modern energy infrastructure improves sites |
With lower overheads and generation capabilities that pay for themselves over time, solar carports enable substantial cost reductions. And as electricity rates rise, solar carports will provide increasing levels of savings each year.
III. Solar Carports are Customizable
One of the key advantages of solar carports is their high degree of flexibility and customization potential. Installers can tailor solar carport solutions to meet the specific needs of the property.
Customization capabilities include:
- Size: Carports can be small or cover expansive lots, with solar panels scaled appropriately
- Layout: Flow with angled parking spots or irregular shapes using creative structural designs
- Solar orientation: Panels can be tilted at ideal angles to maximize sun exposure and power generation
- Aesthetic options: Choose colors/finishes to match branding or surroundings
- Additional features: Integrate lighting, charging stations, storage, signage displays into the carport structure
This modular flexibility empowers property managers to create solar systems tailored to their sites. For example:
- Retail stores can match carport colors to their brand palette
- Fleet yards can install high-capacity carports to power maintenance facilities
- Agricultural facilities can orient solar panels for optimum energy generation across seasons
Customization Factor | Carport Capabilities |
Size | Small or large coverage areas |
Layout | Flow across properties efficiently |
Solar orientation | Optimize panel angle for conditions |
Aesthetics | Match color schemes and branding |
Features | Add lighting, charging, displays |
The adaptable nature of solar carports enables properties to establish renewable energy infrastructure that blends seamlessly with the space. Custom solar carport solutions meet generation needs while fitting aesthetically into the existing environment.
IV. Solar Carports are Easy to Maintain
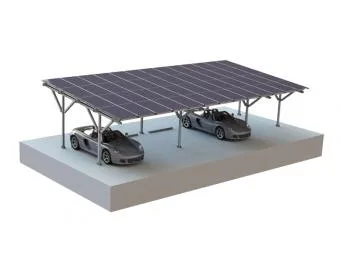
One major advantage of solar carports compared to rooftop solar arrays is that they are much easier to access and maintain. Key factors that simplify upkeep include:
Convenient Access
- Installers can reach panels and electrical components from ground level
- No need for ladders, scaffolding or roof access
- Streamlined inspections, cleaning, repairs
Weather Protection
- Raised canopy structure channels rain, snow melt away
- Prevents to build up of leaves, ice, and other debris
- Prolongs equipment life by shielding from UV and temperature swings
Simplified Connection
- Wiring neatly converges to single interconnection point
- No complex routing through walls and ceilings
- Easy grid integration with net metering
Enhanced Safety
- Grounded access minimizes fall and electrocution risks
- Clearly visible electrical conduits per code
- Stable structures engineered for wind/seismic events
Benefit | Advantage |
Accessibility | Straightforward ground-level component access |
Weather protection | Channels precipitation away, shields equipment |
Simplified wiring | Converges to single interconnection area |
Safety | Reduced risks for installers and inspectors |
The ability to easily reach, assess, maintain, and protect all aspects of solar carports ensures reliable clean power generation over their lifespan. Streamlined upkeep translates into lower operational costs.
V. Solar Carports Provide Protection
Solar carports safeguard vehicles, equipment, and inventory from exposure while also generating clean energy. Key elements of protection include:
Weather Shielding
- Roof structure deflects rain, snow, hail
- Prevents exterior damage, internal water incursion
- Reduces weather-related repairs/clean up
Temperature Control
- Shade cools interior temperatures by over 50°F
- Prevents overheating that strains mechanical parts
- Extends component life by limiting temperature swings
UV Ray Blocking
- Reduces interior fading, cracking, discoloration
- Shields electronics from solar disruption
- Protects tires, seals, plastic components
Shelter from Debris
- Captures falling leaves, airborne dust
- Reduces abrasion, exterior dulling
- Helps maintain asset appearance
Solar carports deliver essential weather protetion to improve durability and lifespan. Shielded assets will look better, require fewer repairs, and maintain optimal working order for longer under a solar canopy.
VI. Solar Carports Generate Clean Energy
Installing solar carports empowers properties to establish renewable energy independence using sun power. Key clean energy benefits include:
Lower Environmental Impact
- Solar carports produce zero direct emissions
- Reduce reliance on fossil fuels for electricity needs
- Support corporate sustainability commitments
Energy Bill Savings
- Lower or eliminate power purchases from utility
- Insulate against rising electricity rates
- Payback financing options often available
Grid Support
- Excess power generation can be sold back to grid
- Stabilize shared infrastructure during high demand
- Enable establishment of micro grids
Enhanced Public Image
- Highly visible sign of commitment to sustainability
- Strengthen community relationships
- Attract forward-thinking customers/partners
Transitioning a portion of power usage to solar carports helps properties minimize environmental impact in an economical way. And their visibility promotes an innovative, eco-conscious public image.
VII. Solar Carports Benefit Businesses
Installing solar carports Structura offers many tangible benefits for companies across sectors:
Cost Reduction
- Lower facility energy bills
- Leverage available parking/storage areas
- Minimize additional weatherproofing spends
Productivity Gains
- Protect inventory and equipment from elements
- Prevent overheating of sensitive materials
- Create comfortable outdoor working conditions
Sustainability Profile
- Highlight green commitment to customers
- Achieve environmental impact goals
- Qualify for related tax/rebate incentives
Grid Independence
- Establish micro grid from carpot output
- Reduce vulnerability to utility outages
- Store excess power in batteries for backup
Customer Experience
- Provide shaded parking for visitors
- Offer EV charging under carport awnings
- Create space for outdoor dining/retail
Forward-thinking companies can leverage solar carports in many ways – from cost and resilience to brand image. The benefits for business operations and the bottom line are substantial.
VIII. Solar Carports Support Communities
Installing solar carports delivers benefits that resonate across neighbourhoods and towns:
Clean Decentralized Power
- Reduce reliance on distant fossil fuel plants
- Establish locally-generated clean energy
- Increase community energy independence
Grid Infrastructure Resilience
- Distribute solar widely across parking lots
- Avoid centralized power failures from single points
- Maintain access to electricity during outages
Civic Collaboration
- Shared public carports in municipal lots
- Joint projects between local stakeholders
- Bring together constituencies around sustainability
Economic Development
- Savings for businesses passed to consumers
- New jobs created in solar installation/maintenance
- Environmental leadership attracts talent relocation
Improved Quality of Life
- Cleaner air from reduced emissions
- Accessible community EV charging
- Vibrant public spaces with carports as social infrastructure
Forward-looking towns are smart to embrace solar carports – they deliver environmental performance, resiliency, and quality of life benefits that serve the whole community.