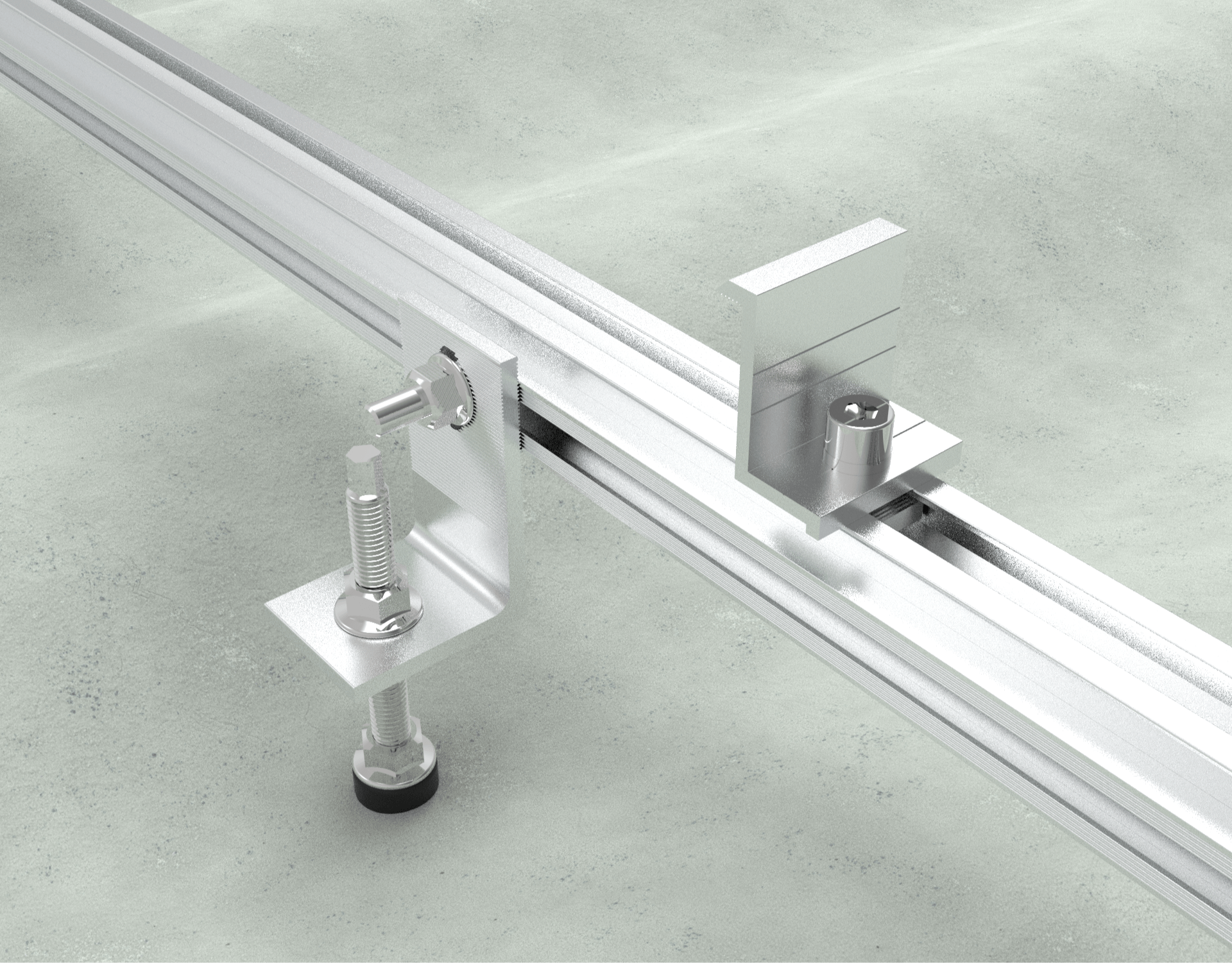
I. Introduction
Hanger bolts are an essential component of solar mounting systems installed on rooftops. They serve as the structural attachment between the solar panels and the roof surface.
Hanger bolts consist of:
- A threaded bolt
- Collar nuts and washers
- An EPDM rubber grommet seal
- A mounting plate with a slot
They are made of durable stainless steel and aluminum.
The key characteristics of hanger bolts include:
Feature | Description |
Adjustability | Offer variable lengths and angles to mount panels |
Structural integrity | Withstand wind, weather and meet building codes |
Watertight sealing | Rubber gasket protects roof from leaks |
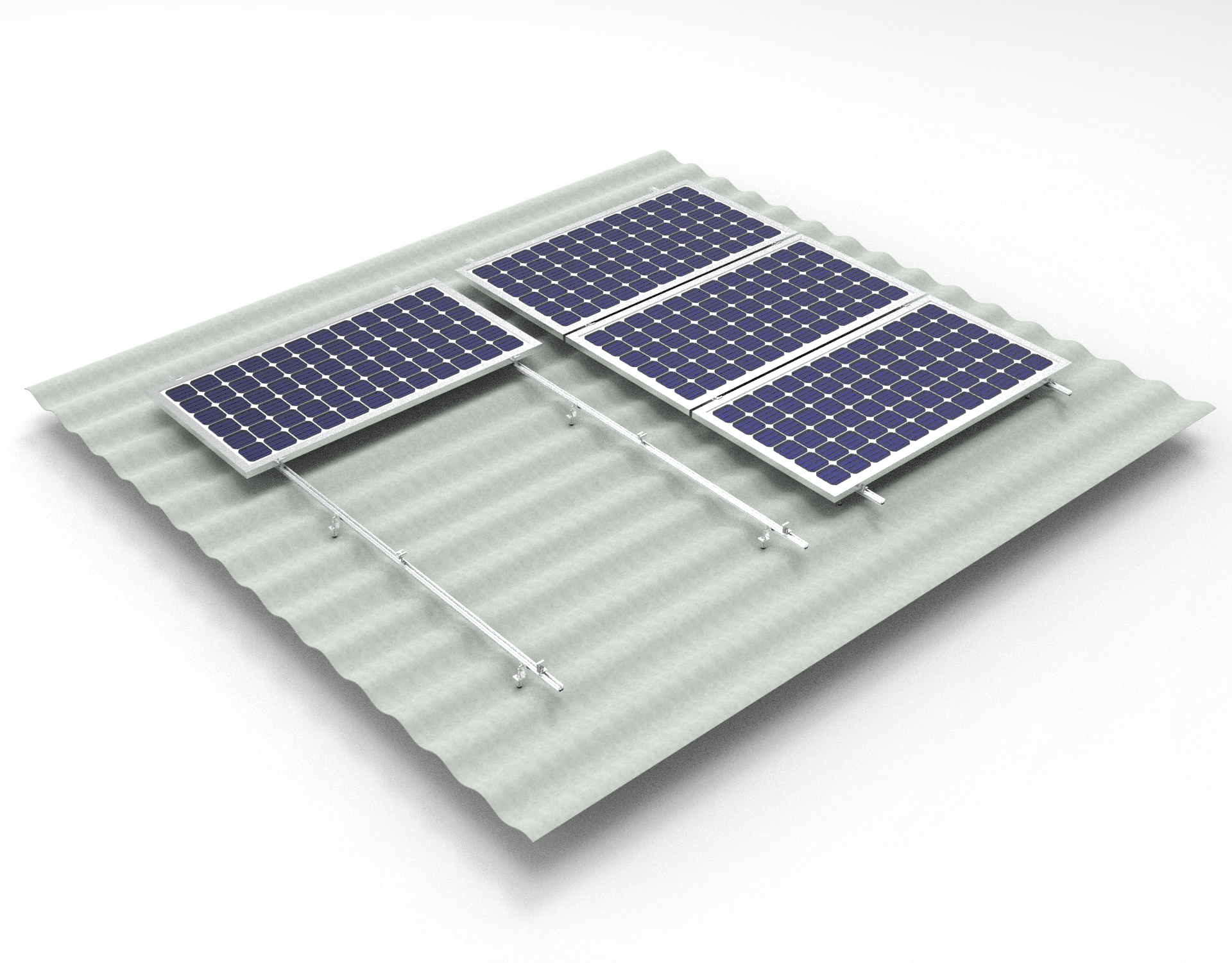
Hanger bolt kits contain all the fittings needed for a complete solar panel installation:
- Hanger screws
- Mounting rails
- Mid/end clamps
We provide a secure and user-friendly mounting system with professionals and DIY installers.
When paired with compatible solar racks and rails, hanger bolt sets enable angled or flat installations on various roof types like singles, tiles, and metal roofing profiles.
By elevating and securely fastening solar modules, hanger bolts play a critical role in durable and high-performing rooftop solar energy systems. Their adjustable nature allows for tailored positioning to maximize solar capture potential.
II. Components
Hanger bolt solar mounting systems comprise three main components that work together:
Hanger Bolts
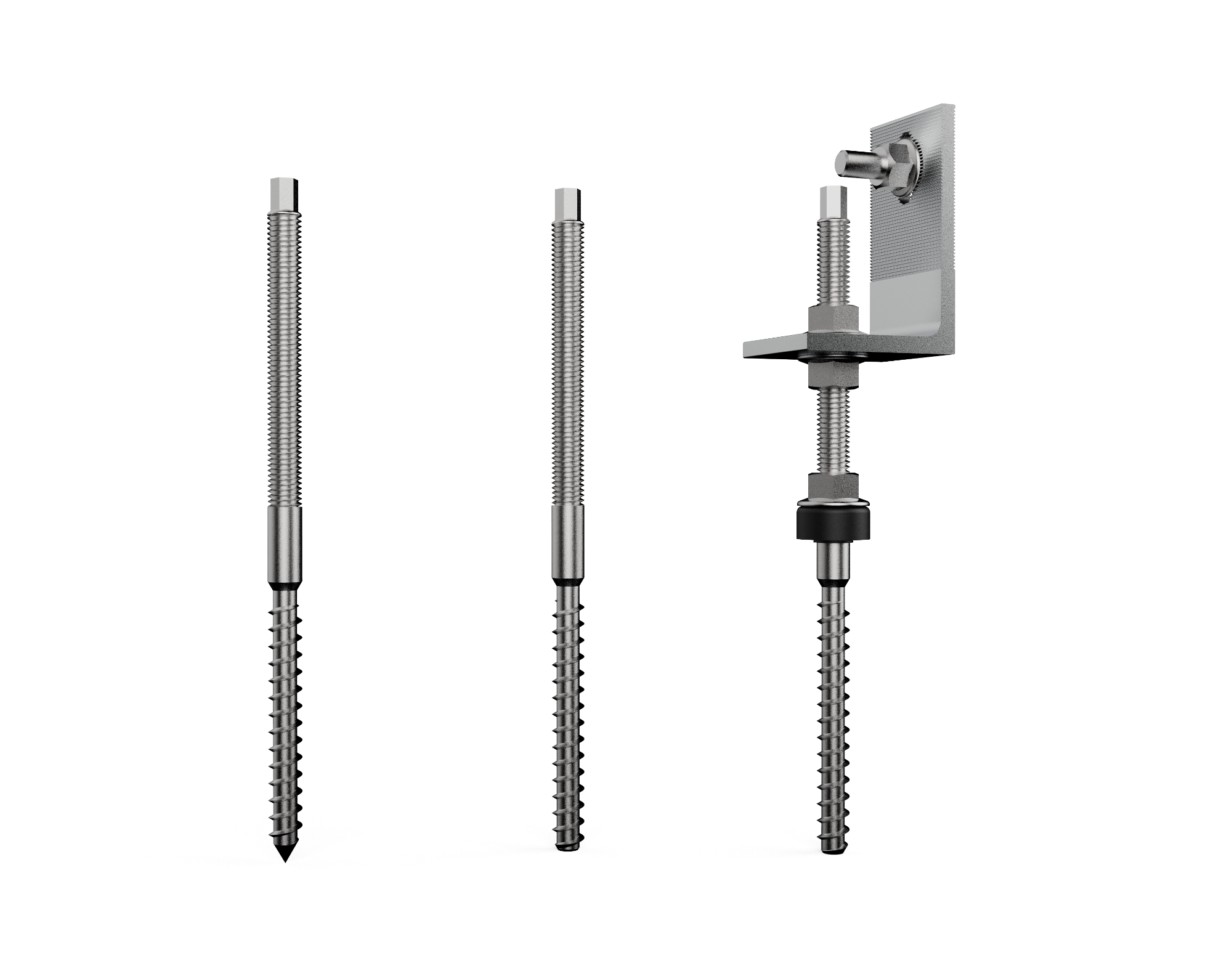
Hanger bolts are the metal fasteners that attach solar panels and rails to the roof structure. Key features include:
- Threaded stainless steel shaft
- EPDM rubber grommets for water sealing
- Flange nuts to secure installation
- Lengths ranging from 7″ to 10″
The function as adjustable “hangers” on the roof to position and elevate PV modules at the optimal tilt and angle. The bolt inserts into a pre-drilled hole in the roof while the gasket provides a tight, weather tight connection protecting roof layers underneath.
Adapter/Mounting Plates

These square adapter plates act as the intermediary between the hanger bolt and solar rail system:
- Made of stainless steel/aluminum
- Slotted holes for adjustability
- Locks into hanger bolt teeth
The plate height is adjustable on the hanger bolt to achieve proper rail height before being locked into place with collar nuts. This flexibility facilitates customized positioning.
Roof Attachments
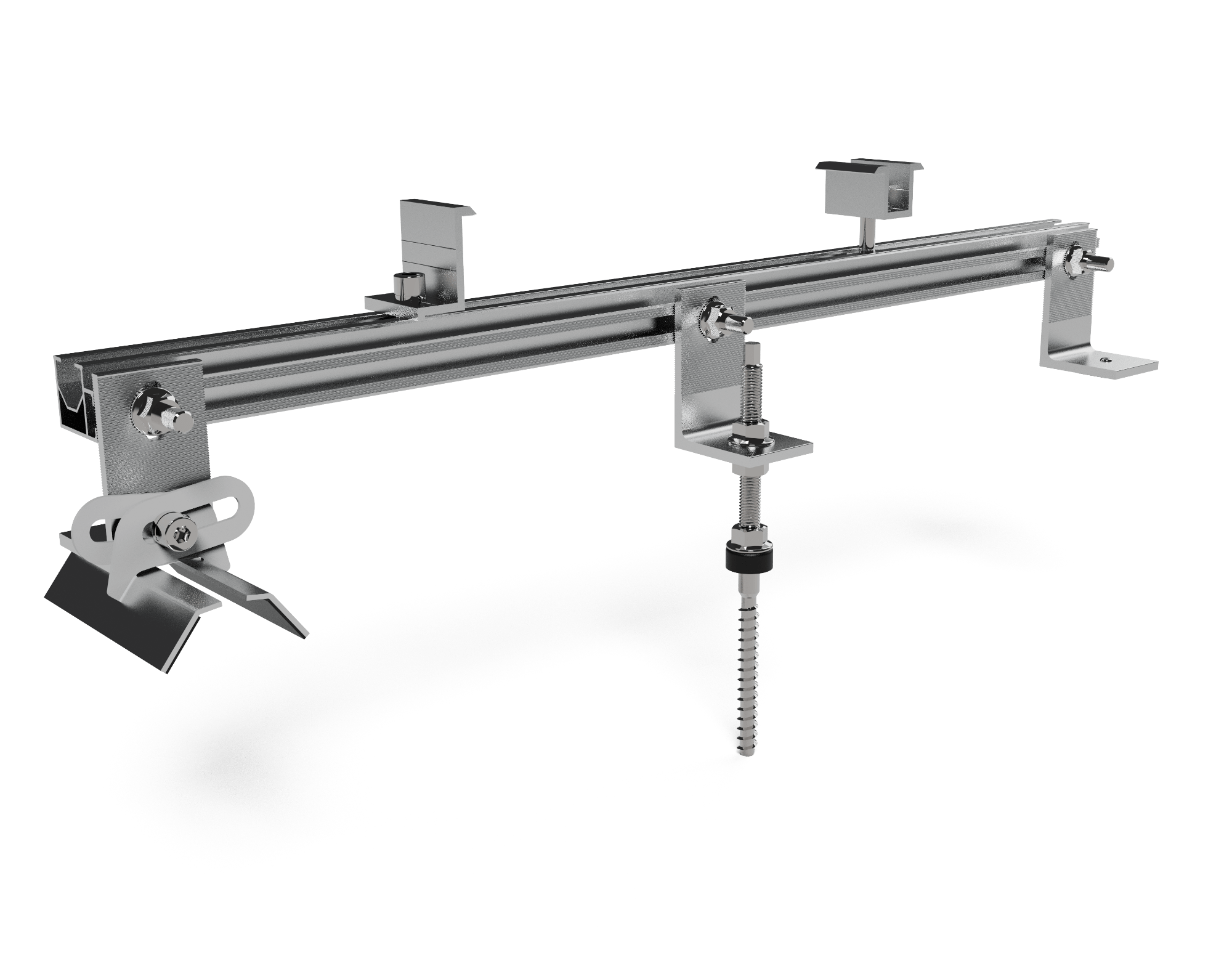
On the underside of the roof, these pieces distribute structural loads:
- Washers
- Support plates with bolt holes
- Solid blocking within roof framing
The arrangement securely anchors the system while protecting roofing materials from excessive loads. This allows the solar panels’ weight to transfer safely from the rails through the hanger bolts into the roof framing via these supportive attachments.
Combined together, these three modular solar mounting system components provide robust structural capabilities for rooftop solar installations.
III. Features and Benefits
Hanger bolt solar mounting kits offer installers and homeowners the following advantageous features and benefits:
Adjustability
- Variable bolt lengths from 150″ to 250″
- Changeable plate heights on the threaded shaft
- Accommodate various roof angles and tilts
- Allow precise positioning of solar modules
This adjustability enables customized installations for maximum sun exposure, output, and performance.
Durability
- Stainless steel and aluminium resist corrosion
- Withstand decades of outdoor/weather exposure
- Rubber gaskets maintain watertight roof seal
- Strong structural connections avoid component failures
The robust metals and secure assembly remain intact for the system’s lifetime, despite snow, wind, rain, UV radiation and temperature swings.
Ease of Installation
- Pre-assembled parts
- Single drilled roof hole per hanger
- Bolt directly into roof structure
- Align plates and rails + tighten into place
The simplified install process reduces labour time and costs compared to alternative attachment methods. No welding or extensive rail alignment needed.
In summary, this customizable, heavy-duty, and DIY-friendly mounting system maximizes the ROI of rooftop solar installations.
IV. Compatibility
Hanger bolt solar mounting systems are compatible with a wide range of roof types and solar panels.
Roof Types
Hanger bolts can secure solar installations onto any common roofing material:
- Asphalt shingles
- Concrete or clay tiles
- Metal panels and roofing profiles
- Corrugated
- Standing seam
- Ribmmed
- Low slope commercial roofs
On tilted roofs, hanger bolts are installed into roof framing rafters or trusses. On flat roofs, concrete blocks anchor the bolts.
EPDM gaskets form tight yet movable seals to accommodate shifting and expansion of roof decks. This protects roof coverings from moisture damage.
Solar Panels
Hanger mounting components work with all major PV panel technologies:
- Monocrystalline
- Polycrystalline
- Thin-film flexible
Systems are designed for longevity to match 30+ year lifespans of solar modules.
Aluminium/steel rails a nd mid/end clamps further ensure universal compatibility – securely holding panels of varying widths and frame types.
No matter the roof covering or solar collection system, hanger bolt sets facilitate adjustable and code-compliant installations. Their versatility makes them widely trusted among installers.
V. Installation Process
Installing a hanger bolt solar mounting system involves a straightforward sequence of steps:
Tools Needed
- Cordless drill
- Torque wrench
- Wrenches for bolt tightening
- Marking pencil
Steps
- Measure and mark pre-drilled holes for hanger placement based on panel layout.
- Insert hanger bolt through roof into rafter and tighten flange nut.
- Add washers and collars to secure in place while allowing bolt to rotate.
- Rotate bolt to desired tilt angle.
- Slide adapter plate onto threaded shaft with slot facing outward.
- Adjust plate to required rail height and tighten collars with torque wrench.
- Secure aluminum mounting rails atop plates, inserting splices to extend.
- Attach mid/end roof clamps and mount solar panels using manufacturer instructions.
This straight-forward installation sequence allows for rapid solar panel mounting while leaving room for full angle and height adjustment.
It’s an easy DIY project for homeowners or professionals alike, made simpler through the hanger bolt system’s user-friendly and pre-assembled parts. Proper torque levels still need adherence to for lasting safety and security.
VI. Performance
Once installed, hanger bolt solar mounting kits deliver exceptional performance and reliability:
Stability
- Withstand wind uplift up to 120 mph
- Resist seismic and dynamic loads
- High shear and pull-out strength
Structural aluminium components and direct roof framing attachments provide robust wind resistance and code compliance.
Weather Resistance
- Metal parts resist corrosion and oxidation
- Rubber seals block water infiltration
- Unaffected by temperature swings, UV rays
Durable metals and gaskets withstand decades of snow, rain, heat and sun exposure.
Waterproofing
- EPDM washers hug roof surface
- Allow proper roof drainage flow
- Protect structural sheathing from leaks
Rubber bushings accommodate shifting while maintaining a watertight connection to underlying roof layers.
In terms of wind/code ratings, all-weather endurance, and moisture protection – hanger bolt framing delivers reliable, top-tier performance year after year. Homeowners gain peace of mind from their investment while collectors benefit from secure solar module support.
VII. Conclusion
The hanger bolt solutions offer a premier solar mounting method that maximizes value for homeowners and installers alike.
Affordability
- Cost-effective hardware
- Straightforward DIY install
- Scalable to any budget
These money-saving features make solar power achievable for most homeowners compared to high-cost racking alternatives.
Aesthetics
- Low profile mounting
- Clean, simple design
- Maintains roofline appearance
Visually appealing, non-invasive placement preserves existing architecture and curb appeal.
Reliability
- Robust metals resist corrosion
- Watertight fit guards against leaks
- Secure stability in storms
Durable components withstand decades of climatic exposure, avoiding failures or repairs.
With streamlined affordability and upkeep combined with strength, adaptability and aesthetic appeal – hanger bolt systems unlock rooftop solar full potential. Their user-friendly nature allows households at all income levels to meet renewable energy goals while adding beauty and resilience.